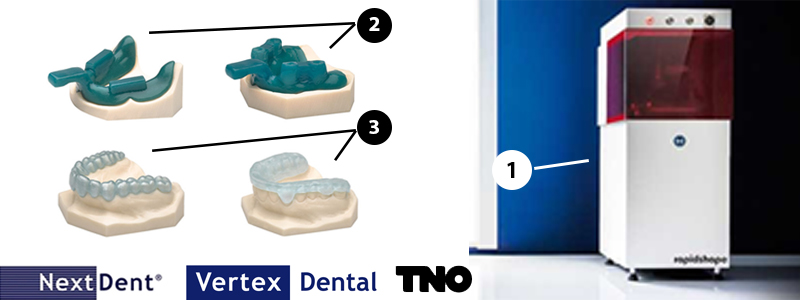
Vertex-Dental is a manufacturer of high quality prosthetic dental products. They provide acrylic materials to vacuum cast teeth, such as the Vertex™ teeth Quint. The Vertex™ teeth grinder can be used to increase the contact surface of the Quint and to place the Quint on a denture base using a bond such as the Vertex™ Acrybond.
Additive manufacturing (AM) simplifies the work flow, teeth don't have to vacuum casted and subsequently milled but can be produced at once.
AM had therefore the potential to disrupt the business model of vertex-dental and posed a threat.
To meet this challenge, Vertex teamed up with TNO. TNO is the largest Dutch governement research institute. TNO had already created the Lepus one, an apparatus for manufacturing a three-dimensional part by solidifying in layers liquid material under the influence of light. The machine uses a special force sensor to speed up the build process. The patents of the machine were sold to a german company called Rapidshape. TNO helped Vertex to adept their materials to be used on the Rapidshape and to get their materials certified. The unique materials can be used for printing custom trays, models, surgical guides, temporary crowns and bridges. Biocompatible materials for dental prostheses, fixed crown and bridge jobs and orthodentic applications will follow soon. The machines of Rapidshape were adapted for the dental market and are sold under the names D30 and D30L.
In figure 1 at the top of this article, the dental printer D30 is shown. A impression spoon is printed on the D30 to take a dental imprint, see figure 2. The dental imprint is inverted via moulding and the inverted model is then scanned. An alternative is to directly scan the mouth using an oral scanner. The D30 can then be used to directly transform the digital model into an orthodontic appliance. Using additive manufacturing, the creation of or orthodentical appliances is sped up rapidly. It reduces the waittime for a patient at the dentist. It also creates cost savings at dental labs, where less technicians are needed to produce a denture. Digital workflow management can be used to achieve greater accuracy and efficiency. Human errors are reduced to a minimum and the entire process can be monitored and managed throughout.